Improve Warehouse Efficiency and Safety with Data Cabling
Properly installed data cabling can significantly enhance warehouse efficiency and promote safety.
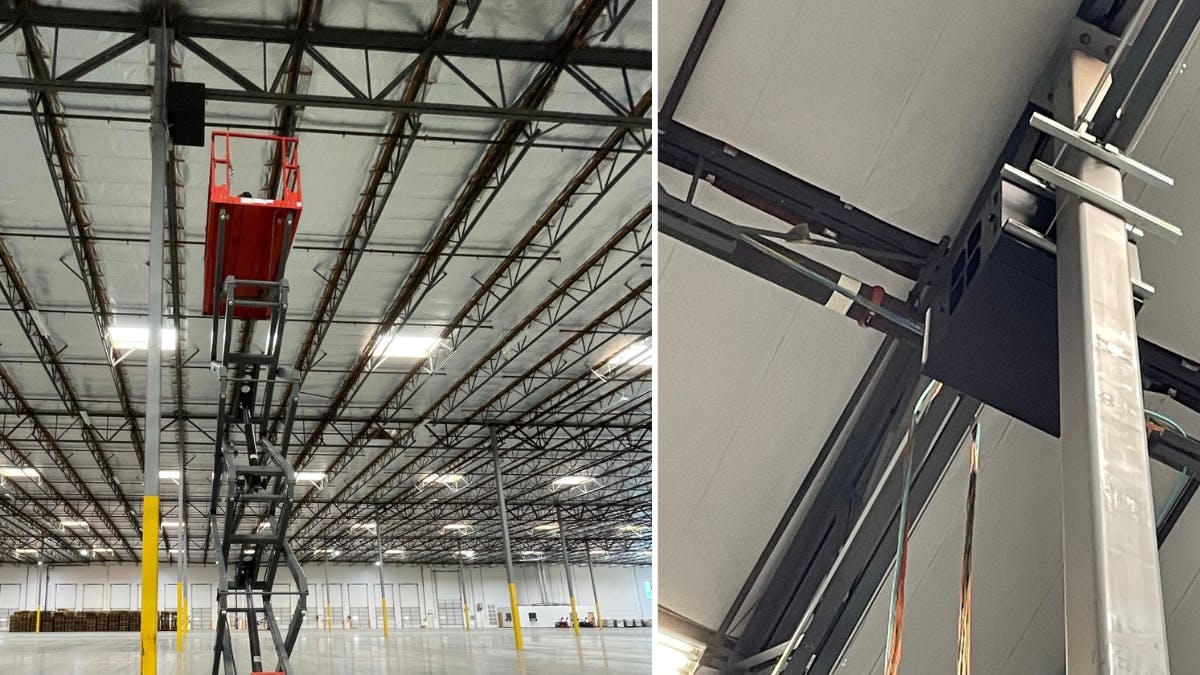
When it comes to improving warehouse efficiency, employee safety is critical. Improperly installed data cabling can create an unsafe work environment, which could put a business at risk for everything from costly lawsuits to lost revenue during shutdowns.
According to the National Safety Council (NSC), the total cost of work injuries in 2021 was $167 billion. This figure is comprised of several different losses, including:
- $47.4 billion in wage and productivity losses
- $36.6 billion in medical expenses
- $57.5 billion in administrative expenses
In addition to the out-of-pocket expense, the NSC reported 103 million days of work productivity lost due to injury. Not only were businesses shelling out big bucks for fees, they were losing the opportunity to make money due to lost working days.
The following outlines seven ways properly installing data cabling creates a more efficient and productive work environment.
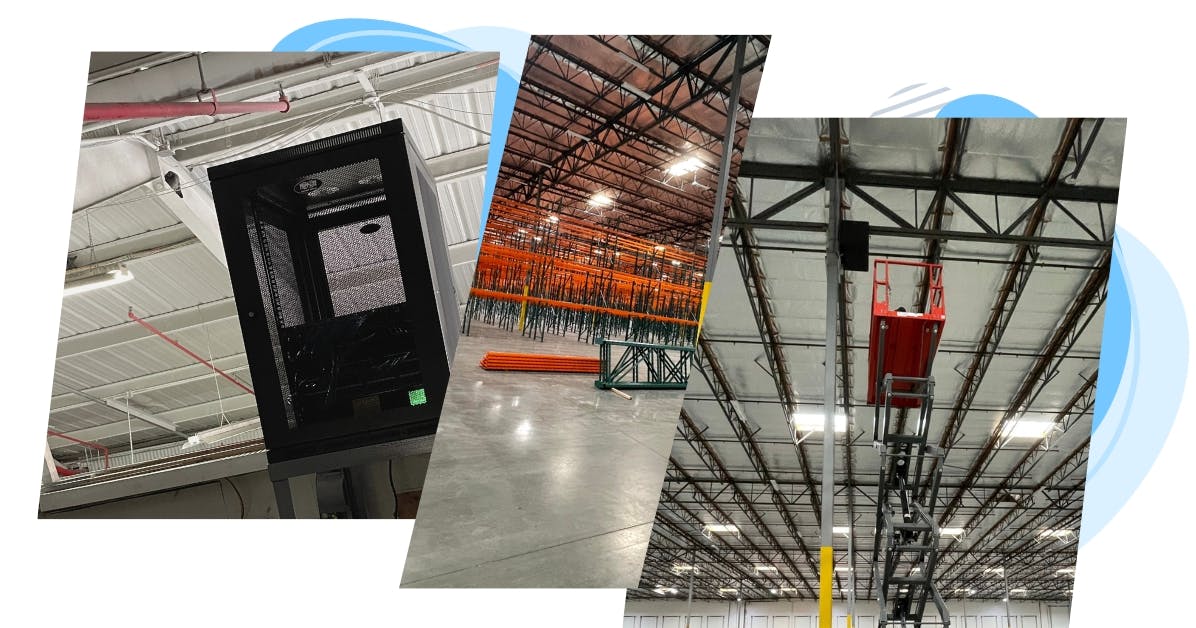
Correctly installing structured cabling and network devices off the floor reduces trip hazards and improves Wi-Fi reception.
7 Ways Properly Installed Data Cabling is Essential in Warehouses
1. Reduced Tripping Hazards
One of the most immediate safety benefits of properly installed cabling is eliminating tripping hazards. Cables that are neatly organized and secured along walls, ceilings, or floors are less likely to obstruct walkways or work areas, reducing the risk of accidents and injuries caused by employees tripping over loose cables.
2. Longer-Lasting Installs
Properly installed cabling is less likely to become damaged or exposed. This helps reduce the long-term maintenance required.
3. Fire Prevention
Loose or damaged cabling can lead to electrical fires if wires become frayed or short-circuited. Properly installed and managed cabling reduces the chances of these events occurring, helping to prevent fires and the resulting damage to goods, equipment, and personnel.
4. Equipment Protection
Well-organized cabling is less likely to be inadvertently pulled or damaged by warehouse equipment like forklifts, pallet jacks, or conveyors. This not only helps prevent downtime caused by cable damage, but also avoids potential safety hazards associated with damaged or exposed wires.
5. Efficient Emergency Response
In an emergency, such as a fire or a medical incident, clear and unobstructed pathways are crucial for swift and safe evacuation. Professionally installed cabling ensures that emergency routes remain clear and accessible, facilitating a more efficient and safer response to critical situations.
6. Compliance with Safety Regulations
Many safety regulations and codes require proper cable management to maintain a safe working environment. Ensuring compliance not only reduces the risk of accidents but also helps a warehouse avoid potential legal and regulatory penalties.
The Occupational Safety and Health Administration (OSHA) has multiple regulations and standards that promote workplace safety. Work surfaces are one of the most significant areas of concern. These are regulated by 29 CFR 1910.22-.30, which recommends, among many things, to avoid clutter.
7. Improved Organization
Beyond safety, organized cabling contributes to a more efficient and productive warehouse environment. When cables are neatly labeled, organized, and secured, it becomes easier for employees to identify and access the necessary connections, reducing downtime and improving overall.
Are You Planning Updates or Upgrades for Your Facilities?
Our team has been serving customers across Southern California since 2006. We understand local codes and the latest best practices in structured cabling. Contact our office, and we're happy to give feedback or costs to make your project a success.